How Wolffkran Arabia helped build the Museum of the Future
S. Neogy ,
27 Feb 2022
Tower crane specialist made iconic project possible with its crane solution, using three Wolff 6531.12 saddle jib cranes, two 355B luffing jib cranes and one 8033.20 saddle jib model in three phases with 20-hour daily shifts

On February 21st, Dubai officially opened the doors to one of the most iconic buildings in the region, indeed even the world – the Museum of the Future. There are few structures on the global architectural landscape that have captured the popular imagination as this marvel of design has. Not only has it become easily recognisable by inhabitants of the UAE, with its majestic presence looming large on Dubai’s main arterial Sheikh Zayed Road, it has also joined the pantheon of wonders that Dubai has built over the last several years.
And a wonder it indeed is. The 77-metre high structure has been envisioned as “a message of hope” by none other than Shiekh Mohammed bin Rashid Al Maktoum, Vice President and Prime Minister of the UAE and Ruler of Dubai. Inaugurating the museum, Sheikh Mohammed said the museum “will be a forum for great minds, scientists, thinkers and experts from around the world”. He envisaged it as a place that will “shape a better future for all of us”.
But building the future is not without its challenges – and building a futuristic structure such as the Museum of the Future was an equally challenging engineering and construction feat. The unprecedentedly abstract and irregular design of the building meant that it demanded special construction materials and techniques – as well as equipment that could rise to the challenge. Enter Wolffkran – the tower crane specialist that supplied not only cranes but lifting solutions to the projects that use its equipment.
The tower cranes used in the construction of the Museum of the Future ever since construction began in 2017 have been Wolff cranes, with Wolffkran Arabia implementing a lifting plan for the project that involved three tower cranes which were erected and then changed to meet the construction needs.
As a crane solution provider, Wolffkran worked with the main contractor BAM International to design lifting operations for the project and keep the operations going through the various stages of the build as the structure’s shape gradually emerged and brought with it more challenges for crane tower operations.
To meet the construction plan and its emerging challenges, the cranes were put up in three phases and Wolffkran Arabia also provided the base design and procedures to erect and dismantle the cranes safely. The company facilitated this process with the SMIE anti-collision systems and in-house trained crane operators.

In the first phase of crane operations starting April 2017, Wolffkran Arabia erected three main tower cranes in three days, one crane a day. They started off with a crane arrangement of three saddle jib cranes – all Wolffkran 6531.12 models with maximum load capacity of 12 tons – operating for the first six months. For identification purposes, the three cranes were called TC1, TC2 and TC3.
The TC1 and TC2 cranes were installed on 2.5m square bases, and the TC3 was installed on a 2.9m square base. Since Wolffkran’s crane bases can be exchanged between all its crane models, installing these bases at the start of the project, permitted for the jacking of the cranes as well as exchanging the cranes for different units on the same base as construction progressed.
The second phase of the crane operations began in October 2017 when the three saddle jib cranes were switched for two 28-ton 355B luffing jib cranes, which was the new TC1 and TC2 and one 20-ton 8033.20 saddle jib crane which was the new TC3.
At the start of phase 2, the cranes elevated 11–12-ton panels but, as construction progressed, they were jacked up to lift up to 20-ton steel parts. The cranes were operated for about 20 hours every day, lifting between 9–15 tons of steel parts every hour. Phase 2 was the longest stage where majority of the construction was done.
For the third and last phase the height under hook of the cranes was increased to 67.5m for TC1 and TC2 and 87.7m TC3 with the jib of TC3 being extended from 45m to 50m to facilitate lifting material of up to 4t. The Museum of the Future project required free standing cranes because of the design of the building and its proximity to the Dubai Metro Red line, where the critical zone is 5m.
Martin Kirby, managing director, Wolffkran Arabia, explains: “We’ve got decades of experience in engineering and operating cranes in confined spaces, usually very close to railway lines and roads. We believe we were chosen for the job because only we could offer a solution to operate high, free standing cranes at the site. We engineered the lifting systems cost effectively with complete control of the operation and without the pressure to offer cheap products or reduced service and support.”
Wolffkran Arabia executed a twofold lifting plan for the Museum of the Future project, involving three tower cranes erected, swapped and jacked up in three different stages. As a crane solution provider, Wolffkran provided the base designs and method statement to erect and dismantle the cranes safely. Wolffkran also integrated the SMIE anti-collision system and handled the logistics involving mobile cranes in coordination with other divisions of Kanoo Group, specifically Johnson Arabia, which has been operating a fleet of mobile cranes for more than 20 years. Wolffkran employed its own in-house trained crane operators.
Giving more details of the lifting plan used by Wolffkran Arabia, Kirby says: “In the first phase, the crane farthest from the Emirates Towers Metro station (TC1) had a jib length of 50m and height under hook (HUH) of 32.6m. The crane closest to the Metro station (TC2) was erected with a jib length of 45m HUH of 23.6m. The crane at the centre (TC3) had a jib length of 50m and HUH of 42.8m.”

Jeffrey Watson, operations director, Wolffkran Arabia, says: “We employed smaller saddle jib cranes to create the concrete podium with 2–3t lifts. During the first stage, the smaller saddle jib cranes enabled us to lift with high speed and efficiency while saving power.”
The third and final stage saw the HUH of the cranes increased gradually to 67.5m (TC1), 67.5m (TC2) and 87.7m (TC3). The jib of TC3 was extended from 45m to 50m. As the project neared completion, the cranes were lifting material of up to 4 tons, and the Wolffkran Arabia team evaluated various scenarios for dismantling the cranes.
“We were thinking about dismantling the cranes before erecting them. Our method statement included a detailed plan for dismantling the cranes after completion of the job. Planning the location of tower cranes should also take into account accessibility for mobile cranes for dismantling the tower cranes. If tower cranes are not designed and positioned correctly by anticipating the challenges of dismantling them after the construction is completed, the costs of dismantling them with mobile cranes will increase significantly,” says Kirby.
The advance planning that factored in the easy dismantling of the cranes given the proximity of the roads and various structures in one of the busiest areas of Dubai, saw the Wolffkran Arabia take down the cranes in smooth, swift and hassle free-operations.
What was left behind was the gleaming wonder of the Museum of the Future – and the satisfaction of being an integral and vital part of an iconic construction project. As Kirby concludes: “While we will miss seeing the Wolff red peeking through the skyline as we drive through that area, we are excited to see the result of a job well-completed.”
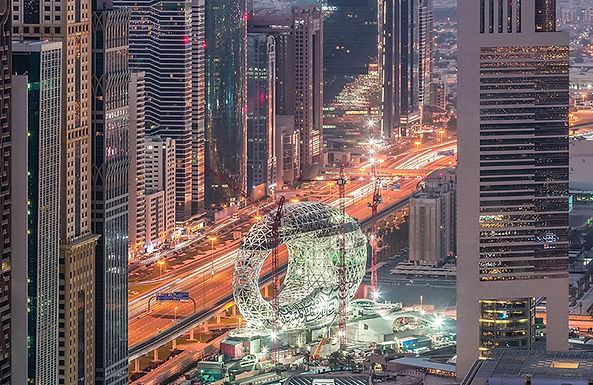